We stand on the brink of a technological revolution that will fundamentally alter the way we live, work, and relate to one another. In its scale, scope, and complexity, the transformation will be unlike anything humankind has experienced before.
Klaus Schwab
Founder and Executive Chairman
World Economic Forum
On our study trip to Automation Valley, we learned about Industry 4.0 and the digitalization of German manufacturing. On the way back to Denmark, one of the other participants said, “yep, the Germans set the standard”. This is indeed the case, even in a very literal sense: They’re making Industry 4.0 a German DIN Standard, and are aiming for international standardization.
Introducing RAMI 4.0
The German Electrical and Electronic Manufacturers’ Association, and its partners, have developed the Reference Architecture Model for Industry 4.0 (RAMI 4.0). Today supported by the Plattform Industrie 4.0 network, RAMI 4.0 is held as a key standard for Industry 4.0.
RAMI 4.0 consists of
a three-dimensional coordinate system that describes all crucial aspects of Industrie 4.0. In this way, complex interrelations can be broken down into smaller and simpler clusters.
The coordinate system is further described as follows:
The “Hierarchy Levels” axis:
Indicated on the right horizontal axis are hierarchy levels from IEC 62264, the international standards series for enterprise IT and control systems. These hierarchy levels represent the different functionalities within factories or facilities. In order to represent the Industrie 4.0 environment, these functionalities have been expanded to include workpieces, labelled “Product”, and the connection to the Internet of Things and Services, labelled “Connected World”.
The “Life Cycle & Value Stream” axis:
The left horizontal axis represents the life cycle of facilities and products, based on IEC 62890 for life-cycle management. Furthermore, a distinction is made between “types” and “instances”. A “type” becomes an “instance” when design and prototyping have been completed and the actual product is being manufactured.
The “Layers” axis:
The six layers on the vertical axis serve to describe the decomposition of a machine into its properties structured layer by layer, i.e. the virtual mapping of a machine. Such representations originate from information and communication technology, where properties of complex systems are commonly broken down into layers.
Together, the axes form a model that can be used as follows:
Within these three axes, all crucial aspects of Industrie 4.0 can be mapped, allowing objects such as machines to be classified according to the model. Highly flexible Industrie 4.0 concepts can thus be described and implemented using RAMI 4.0. The reference architectural model allows for step-by-step migration from the present into the world of Industrie 4.0.
In essense,
…RAMI 4.0 provides a common understanding for standards and use cases….RAMI 4.0 can be regarded as a kind of 3D map of Industrie 4.0 solutions: it provides an orientation for plotting the requirements of sectors together with national and international standards in order to define and further develop Industrie 4.0. Overlapping standards and gaps can thus be identified and resolved.
RAMI 4.0 is referencing three standards:
- IEC 62890 – Life-cycle management for systems and products used in industrial-process measurement, control and automation. Note: Under development since 2013 and not available to the public until its release, scheduled for September 2016.
- IEC 62264 – Enterprise-control system integration.
- IEC 61512 – Batch control.
The International Electrotechnical Commission (IEC) white paper on Factory of the Future explains further that when establishing interoperability in manufacturing environments, different dimensions of integration have to be considered:
- Vertical integration, i.e. along the automation pyramid as defined by IEC 62264/IEC 61512. This includes factory-internal integration from sensors and actuators within machines up to ERP systems.
- Horizontal integration, i.e. along the value chain and throughout production networks. This includes the integration of production networks on the business level as achieved by EDI-based supply chain integration, but might include more in the future, when close-to-real-time and product- or process-specific information is exchanged to increase the level of detail and quality in distributed manufacturing optimization.
- Integration towards engineering and product/production life cycle applications (e.g. IEC 62890) in order to enable low-effort knowledge sharing and synchronization between product and service development and manufacturing environments.
Standardizing RAMI 4.0
RAMI4.0 has now been put forward for standardization in Germany as DIN SPEC 91345 – Referenzarchitekturmodell Industrie 4.0. It often takes years for a DIN SPEC to become an official DIN Standard, but now the process has begun, and since Industry 4.0 seems to be a high priority area for DIN, they may decide to fast-track this standard.
So far, the standard is available in German language only, but should be available in English too soon. For now, the most comprehensive publications in English about RAMI 4.0 seem to be the 2016 status report and the 2015 status report.
IEC has put Industry 4.0, including RAMI, high on their agenda. In their call for their general assembly later this year, IEC outlines its future plans and strategic goals for Industry 4.0 reference models and architectures:
Developing a description of the reference models in dedicated standards. As with core models, reference models are also used in a wide variety of model solutions.
Defining reference models separately as independent standards for the purposes of simplification and avoidance of unintentional deviations, and for better understanding.
Implementing a nearly finished specification (DIN SPEC 91345 – publication planned Q2 2016) as Public Available Specification – PAS within IEC, starting with the new work item procedure in the relevant Technical Committee of the IEC.
The relevant IEC committee would probably be TC65 who also owns the three IEC standards included in DIN SPEC 91345, but there are likely many other TCs in IEC who eventually become involved with Industry 4.0. The same will many other standardization organizations and initiatives. The Technical Management Board (TMB) of the International Standard Organization (ISO) has set up a Strategic Advisory Group (SAG) on Industry 4.0/Smart Manufacturing. This SAG should cooperate closely with the International Electrotechnical Commission (IEC) and the International Telecommunication Union (ITU), and is supposed to report back by September 2016. Most of this work takes place behind closed doors, and the SAGs homepage is not very informative.
Analyzing RAMI 4.0’s roots
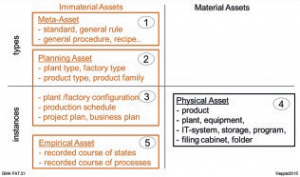
The “Life Cycle & Value Stream” axis is based on an unpublished standard, and therefore difficult to assess. The 2016 status report shed some light on this, and states that:
It was one of the main design decisions of the RAMI4.0 architecture to model type descriptions as individual assets (with own life cycles) which are independent from specific products. To highlight this fact, the assets are divided along the x-axis into “types” (type descriptions) and “instances” (specific products).
And also, that,
This is just a very rough classification but it helps to separate the development and life-cycle management of product types (product families) from the production and lifecycle management of the individual products.
The distinction between type and instance is classic in software engineering and information modeling. RAMI 4.0 maps the asset categories to the life-cycle dimension and the value stream.
Architecturally, this is an interesting approach. But someone really needs to work on the visualization and explanation of the dimension. The status report hints that the IEC 62890 standard will explain it all.
The “Hierarchy Levels” (with IEC62264) dimension is based on the classic ISA-95 which dates back to the 1990s (but is still maintained).
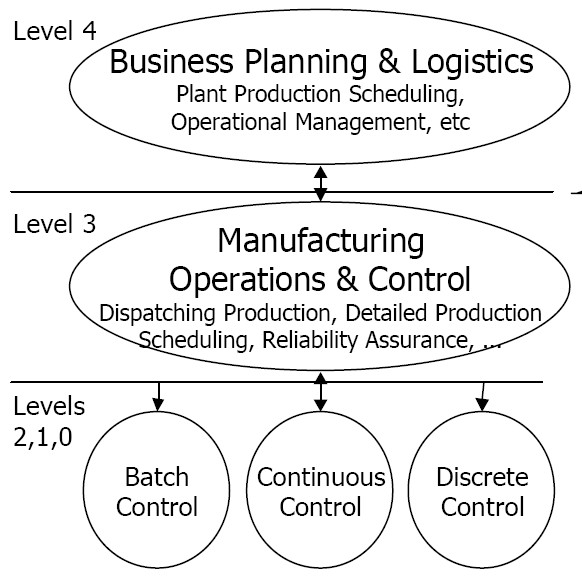
ISA notes that the purpose of ISA-95 is:
To create a standard that will define the interface between control functions and other enterprise functions based upon the Purdue Reference Model for CIM (hierarchical form) as published by ISA. The interface initially considered is the interface between levels 3 and 4 of that model. Additional interfaces will be considered, as appropriate. The goal is to reduce the risk, cost, and errors associated with implementing these interfaces. The standard must define information exchange that is robust, safe, and cost effective. The exchange mechanism must preserve the integrity of each system’s information and span of control.
The Purdue Reference Model for CIM (Computer Integrated Manufacturing) from 1989, published as ISA-95, became the de facto organizing logic for manufacturing information systems and defined that the 0-4 levels have core information systems: ERP at level 4, MES at level 3, and SCADA at level 2.
The hierarchy in RAMI 4.0 is divided into two parts: products (and users) and equipment (field devices, control devices, stations, work units, enterprises and connected world).
The status report seems to acknowledge that RAMI 4.0 may not have hit the nail:
All in all, the ordering schema along the y-axis is just a presentation help for fostering an intuitive understanding of the architecture. In case the terms or aggregation steps do not fit into the respective domains, they can easily be readjusted.
The “Layers” axis
serve to describe the decomposition of a machine into its properties structured layer by layer, i.e. the virtual mapping of a machine. Such representations originate from information and communication technology, where properties of complex systems are commonly broken down into layers.
Layering is a classic theme in enterprise architecture. Although there are some critics, most current enterprise architecture frameworks use architectural layers (e.g., strategy, business, information, applications, infrastructure, and security in EA3).
“The nice thing about standards …”
“…is that you have so many to choose from,” Tanembaum‘s old “joke” about standardization, applies here: RAMI 4.0 is not the only standard for digital industry reference architecture.
The major other standard is the Industrial Internet Reference Architecture (IIRA) from the Industrial Internet Consortium, which is
the open membership, international not-for-profit consortium that is setting the architectural framework and direction for the Industrial Internet. Founded by AT&T, Cisco, GE, IBM and Intel in March 2014, the consortium’s mission is to coordinate vast ecosystem initiatives to connect and integrate objects with people, processes and data using common architectures, interoperability and open standards.
IIC is established by the Object Management Group (OMG). Many architects use OMGs modeling standards, including the Unified Modeling Language (UML), Business Process Model and Notation (BPMN) and Model Driven Architecture (MDA).
IIRA is presented as follows:
This Reference Architecture is a statement of what the most important Industrial Internet architecture components are, how they fit together and how they influence each other. It reflects consensus on major architecture questions among participants from energy, healthcare, manufacturing, transportation and public sectors.
I will look closer at IIRA in a future blog post.
IIC and Plattform Industrie 4.0 in March 2016 announced that they will work together to align RAMI 4.0 and IIRA – Cooperation Among Two Key Leaders in the Industrial Internet – see press release and blog. They released some initial mappings:
Industrial cultures and their “movements”
RAMI 4.0 and IIRA are the two major deliverables from the two “movements”, Industrie 4.0 and the Industrial Internet. Representatives from these “movements” were brought together in a panel here the other day at the Hannover Messe, and a report, BAM! POW! Industrie 4.0 Meets the Industrial Internet!, notes that
In the end, the panel did not agree on whether there would be ultimately one platform or many. But they did agree that they share a common view on the need to gain an understanding of how things should function and making sure that they interact.
Kris Bledowski from the US-based Manufacturers Alliance for Productivity and Innovation compared the movements about a year ago:
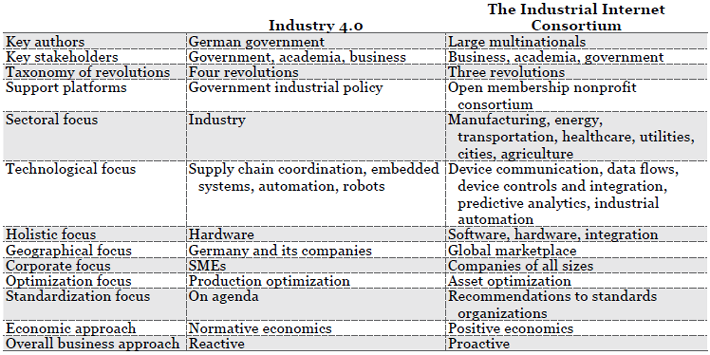
Bledowski sums it up:
- Industrie 4.0 strives to optimize production while the IIC’s research targets returns to any asset
- Industrie 4.0 works on standardization whereas the IIC works on enabling platforms that might set future standards
- Industrie 4.0 is reactive to a fast pace of high-tech innovation; the IIC proactively pushes the frontier of any internet-enabled application
Generalizing the Reference Architectures
The Purdue Reference Model is a key element in PERA, the Purdue Enterprise Reference Architecture, the early 1990s reference model for enterprise architecture. PERA is an example of what was then called Reference Architectures of type II. Other such architectures were GRAI-GIM and CIMOSA.
Over the years, many other “industrial” reference architectures have been established. Many of these are sector-specific. For example, in the oil industry, POSC Caesar Association (PCA) and MIMOSA have established PCA-MIMOSA Reference Architecture Framework for Integrated Engineering and Operations in 2013. It describes
a reference architecture for defining, designing and classifying IT applications, systems and infrastructure in the upstream oil and gas industry, downstream petrochemical industry, and for engineering, procurement and construction projects.
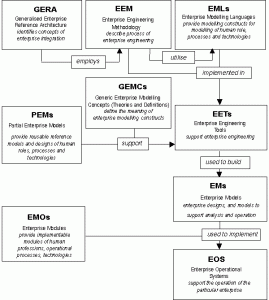
In 1994 then came the Generalised Enterprise Reference Architecture and Methodology (GERAM), which also comprises a framework and methodology. GERAM became part of ISO 15704 “Requirements for Generalised Enterprise Reference Architectures and Methodologies” in 2000.
Fast forward, and many frameworks and methodologies later, GERAMs authors did a recent review of the last 20 years with reference architectures, and observed,
We believe that the future of EA is in its ability to develop an interdisciplinary language and theory enabling a concerted and synergistic application of contributions of underlying disciplines (results from management science, systems, industrial, manufacturing and software engineering, IS, Artificial Intelligence, and so on).
GERAM is a valuable baseline meta-framework – to discuss the above, to create new theories, schools of thoughts, integration of engineering practices and tools, explanations of how technologies can be part of EA, methodologies for EA implementation, and Partial and Particular models for re-use.
As discussed in a previous blog post, and explored in a Special Issue on Future Perspectives On Next Generation Enterprise Information Systems of the Computers in Industry journal, we need to renew our reference architectures and architectural practices:
No doubt that the next generation of enterprise information systems will continue emphasising the need for scalable, reliable, extensible, flexible, highly available and maintainable systems architectures providing ubiquitous, plug-and-play, secure, interoperable and networked solutions to realise smarter and collaborative systems, platforms and ICT infrastructures for all entities operating in a common business ecosystem.
The reference architectures we define and use must reflect our architectural visions. RAMI 4.0 and IIRA are two different visions. Which one will be best? As we architects always say, “it depends”.